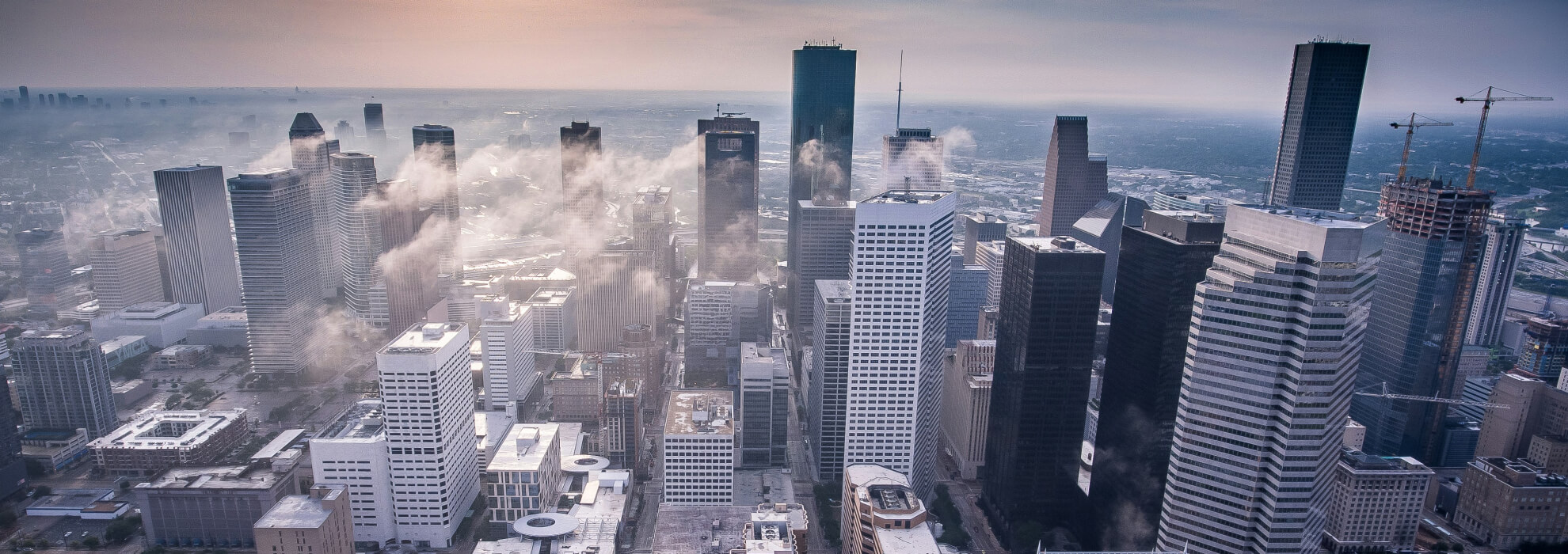
Watch short for this article (5 slides)
Cement's Concrete Climate Problem: Innovations Aiming to Decarbonize Construction
Cement, the essential binder in concrete, is the literal foundation of modern infrastructure and the second most consumed substance on Earth after water. However, its production is exceptionally carbon-intensive, accounting for a staggering **7-8% of global anthropogenic CO₂ emissions**. As the world grapples with the climate crisis, decarbonizing this critical industry has become a paramount challenge. Driven by regulatory pressure, market demands, and technological ingenuity, a wave of innovation is sweeping through the sector, offering pathways to drastically reduce cement's environmental footprint. Companies like Fortera, alongside numerous others, are pioneering approaches ranging from carbon capture and utilization (CCU) to entirely new binder chemistries, signaling a potential revolution in how we build our world.
Deconstructing Cement's Carbon Footprint: Why is it So High?
The immense carbon footprint of traditional **Portland cement** production stems primarily from two unavoidable aspects of its manufacturing process:
- Process Emissions from Calcination (~50-60% of total cement CO₂): This is the largest source and inherent to the chemistry. Limestone (primarily calcium carbonate, CaCO₃) is heated to extremely high temperatures (around 1,450°C or 2,640°F) in a rotary kiln. This intense heat causes a chemical reaction called calcination, breaking down the limestone into calcium oxide (CaO, or lime, the key ingredient in clinker) and releasing massive amounts of CO₂ directly into the atmosphere.
CaCO₃ (Limestone) + Heat → CaO (Lime) + CO₂ (Process Emission)
- Combustion Emissions from Fuel (~30-40% of total cement CO₂): Achieving the necessary high temperatures in the kiln requires burning vast quantities of fuel. Historically, coal and petroleum coke have been the dominant fuels, releasing significant CO₂ upon combustion. While alternative fuels (biomass, waste materials) are increasingly used, substantial combustion emissions remain.
- Electricity and Transport Emissions (~5-10% of total cement CO₂): Energy is also consumed for grinding raw materials and the final cement product, operating equipment, and transporting materials and finished products.
Addressing cement's climate impact therefore requires tackling both the chemical process emissions and the energy-related emissions simultaneously. (IEA - Cement Sector Overview)
Innovating Beyond Portland: Pathways to Low-Carbon Cement
A diverse portfolio of solutions is emerging, targeting different stages of the production process or offering entirely new chemistries:
1. Enhancing Efficiency and Fuel Switching
These are often the first steps taken by industry:
- Kiln Upgrades & Waste Heat Recovery: Improving the thermal efficiency of kilns and capturing waste heat for power generation or other uses.
- Alternative Fuels: Substituting fossil fuels with lower-carbon alternatives like biomass, processed sewage sludge, or non-recyclable industrial wastes. While helpful, this primarily addresses combustion emissions, not the larger process emissions from calcination.
2. Reducing the Clinker Factor (Clinker Substitution / Blended Cements)
Since clinker production (via calcination) is the main emissions source, replacing a portion of it with other materials (Supplementary Cementitious Materials - SCMs) significantly reduces the overall footprint.
- Traditional SCMs: Fly ash (a byproduct of coal combustion) and ground granulated blast-furnace slag (GGBS, a byproduct of iron production) have long been used. However, their supply is finite and potentially declining as coal power and traditional steelmaking decrease.
- LC³ (Limestone Calcined Clay Cement): A highly promising technology blending clinker with **calcined clay** (clay heated to moderate temperatures, ~700-850°C, much lower than clinker production) and ground **limestone**. The calcined clay reacts synergistically with the limestone and clinker hydration products, allowing for clinker replacement ratios of up to 50% while maintaining good performance. This can reduce CO₂ emissions by **up to 40%** compared to standard Portland cement. Clay and limestone are abundant globally, making LC³ highly scalable. (LC3 Technology Resource Centre)
3. Carbon Capture, Utilization, and Storage (CCUS)
This involves capturing CO₂ emissions generated during production and either storing them permanently underground (CCS) or using them to create valuable products (CCU).
- Post-Combustion Capture: Using chemical solvents (like amines) to scrub CO₂ from the kiln flue gas after combustion. Requires significant energy for solvent regeneration (the "energy penalty").
- Oxy-Fuel Combustion: Burning fuel in pure oxygen instead of air produces a flue gas highly concentrated in CO₂, making capture easier. Requires an energy-intensive air separation unit.
- Integrated Capture/Utilization Processes (e.g., Fortera): Fortera’s process captures kiln exhaust gas and uses the CO₂ to carbonate reactive calcium silicate minerals (or potentially reactive magnesium oxide) under specific conditions, creating a cementitious powder. This material can replace traditional cement, effectively mineralizing the captured CO₂ within the product itself. Fortera claims this process can reduce overall CO₂ emissions by **up to 70%** by both avoiding calcination emissions for the portion replaced and utilizing captured CO₂. (Fortera Technology Overview)
- CO₂ Utilization in Concrete (e.g., CarbonCure, Solidia):
- CarbonCure: Injects captured CO₂ (often sourced from industrial emitters, potentially DAC in future) into fresh concrete during mixing. The CO₂ reacts with cement to form calcium carbonate nanoparticles, strengthening the concrete (potentially allowing less cement to be used) and permanently mineralizing the CO₂. Typically achieves a **5-10% reduction** in the concrete's carbon footprint primarily through cement reduction and mineralization.
- Solidia Technologies: Produces a lower-emission calcium silicate cement binder and replaces traditional water curing with a patented CO₂ curing process. CO₂ reacts with the cement to harden the concrete, sequestering carbon within the final product. Claims significant reductions (potentially up to 70% across production and curing) but requires specialized curing chambers.
4. Novel Binder Chemistries (Moving Beyond Portland Clinker)
These approaches aim to replace Portland cement entirely with binders that have inherently lower or even zero process emissions.
- Geopolymer Cements: Formed by reacting aluminosilicate precursors (materials rich in silicon and aluminum, like fly ash, slag, or calcined clays/natural pozzolans) with an alkaline activating solution (e.g., sodium hydroxide, sodium silicate). This process avoids limestone calcination entirely. Potential CO₂ reductions can be **80-90%** *if* the precursors are readily available industrial byproducts or efficiently produced natural materials, and the alkaline activators are produced using low-carbon energy.
- Magnesium-Based Cements: Various types exist, including Magnesium Oxychloride (MOC), Magnesium Phosphate Cements (MPC), and cements based on reactive Magnesium Oxide (MgO). Some reactive MgO cements can be produced at lower temperatures than Portland clinker and have the potential to absorb atmospheric CO₂ *after* placement through natural carbonation, potentially leading to carbon-neutral or even carbon-negative materials over their lifecycle.
- Other Chemistries: Research explores calcium sulfoaluminate (CSA) cements, belite-rich cements, and other novel formulations that require less limestone or lower production temperatures.
Comparing the Pathways: Potential and Hurdles
Each approach offers different advantages and faces unique challenges:
Technology Pathway | Est. CO₂ Reduction Potential (vs. OPC*) | Technology Readiness Level (TRL) | Key Advantages | Key Challenges & Considerations |
---|---|---|---|---|
Efficiency / Fuel Switching | 5-15% | High (Mature) | Proven; relatively easy to implement | Insufficient alone for deep decarbonization; alternative fuel availability/cost. |
Clinker Substitution (SCMs) | 10-30% (Traditional SCMs) Up to 40% (LC³) |
High (SCMs) Med-High (LC³) |
Proven performance (SCMs); Abundant materials, high potential (LC³) | SCM supply constraints; need for standards/acceptance for LC³. |
CCUS (Capture & Store/Utilize) | Potentially 50-90%+ (depending on capture rate & application) | Medium (Post-combustion) Med-Low (Integrated/Novel) |
Can address process emissions directly; utilization creates value. | High cost (CAPEX/OPEX); energy penalty (must use clean energy); CO₂ transport/storage infrastructure; utilization market scale; permanence verification (utilization). |
Novel Binders (Geopolymers, Magnesium-based, etc.) | Potentially 70-90%+ | Low-Medium | Eliminates/reduces calcination; potential for carbon negativity (some Mg-based). | Raw material availability/consistency; activator production footprint; cost; lack of long-term data/standards; market acceptance. |
*OPC: Ordinary Portland Cement. Reduction potentials are indicative and vary widely based on specific processes, materials, energy sources, and system boundaries. TRL varies within categories.
Overcoming Barriers to Scale: Paving the Way for Green Concrete
Transitioning the massive global cement industry requires overcoming significant hurdles:
- Cost Competitiveness: Many low-carbon technologies currently carry a "green premium." Reducing costs through R&D, economies of scale, and supportive policies (like carbon pricing) is essential.
- Standards and Specifications: Construction codes are often prescriptive, based on decades of experience with Portland cement. Updating standards to performance-based specifications that allow for novel binders and blends based on proven durability and strength is crucial but takes time.
- Capital Investment Cycles: Cement plants are huge investments with long lifespans (40+ years). Retrofitting existing plants (e.g., for CCUS) is expensive, and building entirely new plants based on novel chemistries requires massive capital commitment and risk tolerance.
- Supply Chain Development: Scaling up alternatives like LC³ or geopolymers requires developing reliable supply chains for consistent quality raw materials (e.g., calcined clay, fly ash, slag, activators). For CCUS, infrastructure for CO₂ transport and storage/utilization is needed.
- Market Acceptance: Building confidence among engineers, architects, developers, and contractors regarding the long-term performance and durability of new cementitious materials is vital. Demonstration projects and transparent data sharing are key.
The Policy and Collaboration Imperative
Accelerating the transition necessitates strong policy drivers and collaboration:
- Carbon Pricing & Regulation: Implementing meaningful carbon prices or emissions standards makes low-carbon options more competitive.
- Green Public Procurement: Governments specifying or incentivizing the use of low-carbon concrete in public infrastructure projects creates crucial early market demand.
- R&D Funding and Incentives: Supporting research, development, and deployment (RD&D) of promising technologies through grants, tax credits (like 45Q for CCUS in the US), and loan programs.
- Industry Roadmaps: Collaborative efforts like the Global Cement and Concrete Association (GCCA) Concrete Future Roadmap outline pathways and commitments towards carbon neutrality.
- Circular Economy Integration: Promoting the use of waste materials as SCMs or alternative fuels, and designing structures for easier deconstruction and material reuse.
Conclusion: Building a Sustainable Foundation
The cement and concrete industry stands at a critical juncture. Faced with the undeniable need to decarbonize, it is responding with a remarkable surge of innovation. From optimizing existing processes and substituting clinker with materials like calcined clay, to pioneering carbon capture and utilization systems like Fortera's, and developing entirely new binder chemistries, multiple pathways toward low-carbon and even carbon-neutral concrete are emerging. While significant challenges related to cost, scale, standards, and infrastructure remain, the combination of technological advancement, supportive policy, and industry collaboration offers a clear route forward. Successfully navigating this transition is not just an industrial challenge; it is fundamental to building the sustainable infrastructure required for a climate-resilient future.